Materials Used for Forging
Forging is process that metal is flatten, thumped or extruded for acquiring high strength. In general, the metal should be preheated to the prospective temperature before forging. What should be noticed that forging and casting are different. Forging is not like casting that the metal is poured after being molten.
Compared with metal parts made by other metal processing methods, forgings have higher strength. So, forgings are usually chosen for higher requirements for reliability and security. However, normally, forgings are less used as internal assembling components, applied in aircraft, automobile, tractor and shipping, oil drill equipment, engine, missile and other main equipment.
Forgings have diversification on dimension, shape and complication, ranging from hammer and spanner inside tool cabinet to the components having precise tolerance applied in Boeing 747 and space shuttle of NASA. Actually, 18,000 parts used in Boeing 747 are forgings. Other main applications include aviation, defense, automobile, agriculture, construction, mining, material transmission and general industrial equipment. Annual sales of custom forging, the largest forging industry exceed 6 billion dollars. Those custom forgings are made by about 250 of 350 forging enterprises from the U.S., Canada and Mexico.
Almost all of metals can be forged. But, commonly used metals include carbon steel, alloy, stainless steel, tool steel, aluminum, titanium, brass, copper and high temperature alloy containing cobalt, nickel and molybdenum. Every metal has its own strength and weight. Based on different features, different metals are used for special parts to meet customers' requirements.
Materials used for forgings are mainly carbon steel and alloy steel having different contents. Other metals are aluminum, magnesium, copper, titanium and their alloys. Initial status of materials are bar, ingot casting, metal powder and liquid metal. The ratio between cross sectional area before deformation and cross sectional area after cross sectional area is called as forging ratio. Properly choosing forging ratio, reasonable heating temperature and soaking time, initial forging temperature and final forging temperature, proper deflection and strain rate have great influences on improving product quality and reducing cost.
Common medium and small forgings use circular or square bar as blanks. Bar has homogeneous grain structure, good mechanical properties, precise shape and dimension, good surface quality, convenient for mass production. Only properly controlling heating temperature and deformation conditions, forgings having good performances can be made out without much forging deformation.
Ingot casting is only used for large forgings. Ingot casting is as-cast structure, having large columnar crystals and loosen core. So, columnar crystals should be broken into fine grains through large plastic deformation, pressing loosen core into tight core so that good metal tissue and mechanical properties can be acquired.
Powder metallurgy performed blank having been pressed and sintered can be made into powder forgings parts through no-flash forging in hot state. Powder forgings are closed to the density of common forgings, having good mechanical properties and high precision, which can reduce the following cutting. Powder forgings have homogeneous inner tissue without segregation, which can be used to manufacture small gear or other parts. However, the price of powder is higher than the price of common bar. The application is limited in production.
Apply static pressure on liquid metals which poured on impression, making liquid metals solidify, crystallize, flow, plastic deform and form under pressure, then, die forgings having required shape and properties can be acquired. Liquid metal forging is a forming method between die casting and die forging, particularly suitable for complicated thin-wall part which that general die forging forms difficultly.
Besides general materials, iron base high temperature alloy, nickel base high temperature alloy and cobalt base high temperature alloy also can be forged or rolled. However, those alloys have quite narrow plastic zone. So, forging difficulty is relatively large. There are strict requirements for heating temperature, initial forging temperature and final forging temperature of different materials.
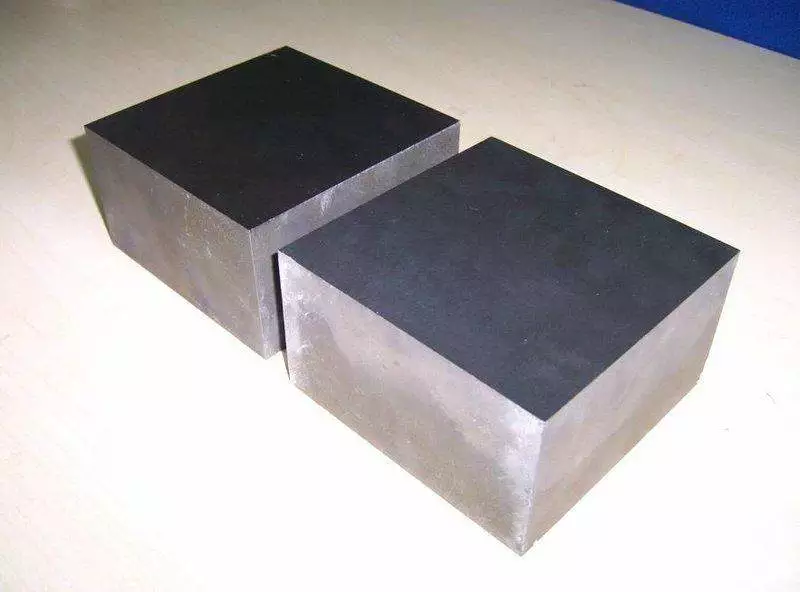