Forged connecting rod for engine.
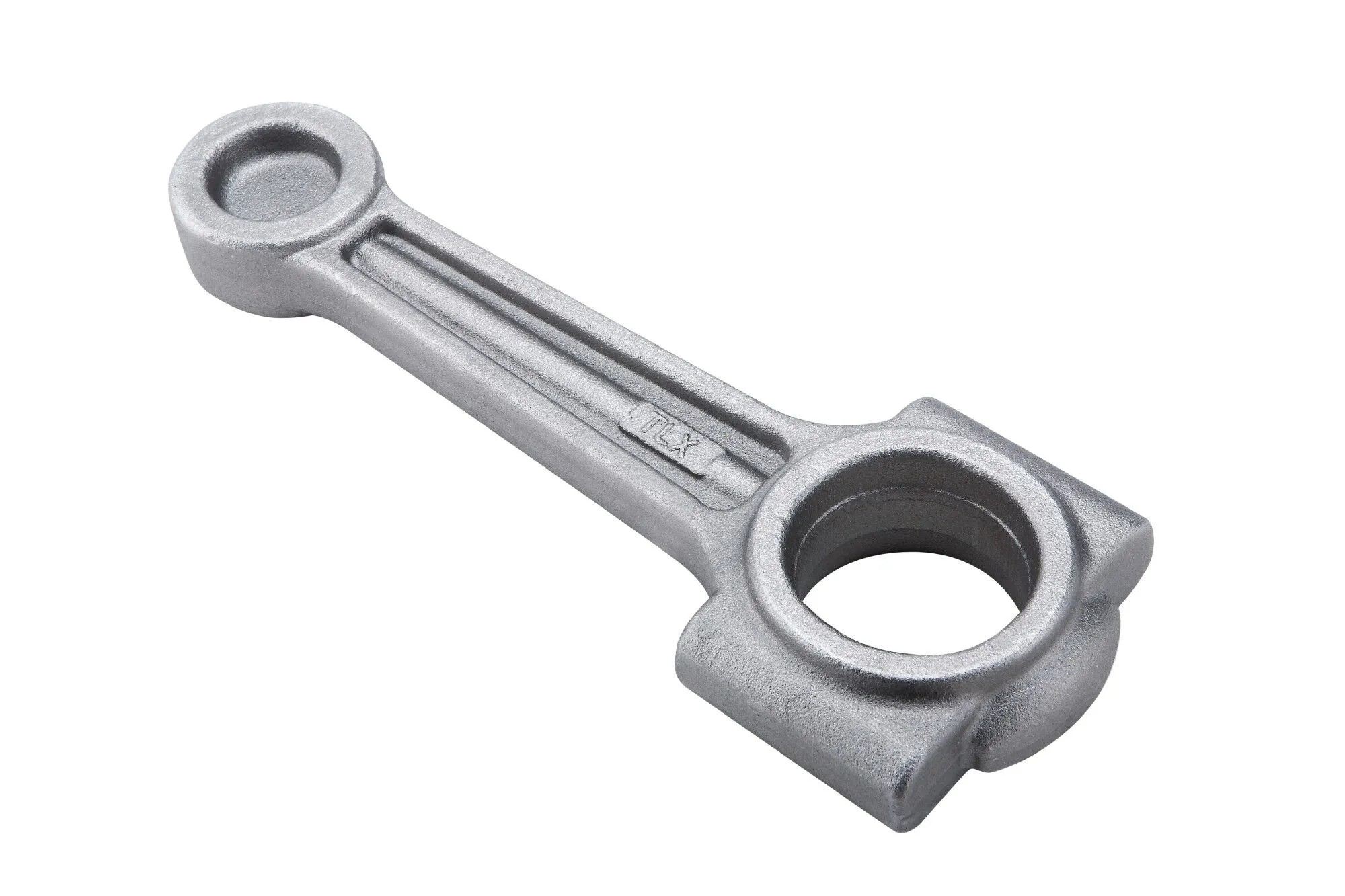
Key Specifications / Features
Hits: 59
Connecting rod connects the piston and the crankshaft, and transmits the force exerted by the piston to the crankshaft, transforming the reciprocating motion of the piston into the rotational motion of the crankshaft. It is one of the main transmission components of automotive engines, which transmits the pressure of the expanding gas of the piston to the crankshaft, transforming the reciprocating linear motion of the piston into the rotational motion of the crankshaft, in order to output power.
Request a quote
Tags
Detail Information
Name:Connecting rod
Process:Forging.Machining.Heat treatment.Surface treatment.
Raw material:ASTM1035,ASTM1045,ASTM1021,ASTM1040,ASTM1320/20Mn2,ASTM1340/40Mn2,ASTM5120/20Cr,ASTM5140/40Cr,ASTM4119/20CrMo,ASTM4140/42CrMo,ASTM4135/35CrMo,ASTM4340/40CrNiMo,ST52-3/Q355/16M
Weight Range:0.1-200kgs
Certificate:ISO/TS16949
Heat treatment::Normalizing,Quenching and tempering
Inspection:Magnetic Powder Defects Test, Hardness Test, Dimension Test
Structure and function of connecting rod.
It is composed of three parts: big end of connecting rod,rod body and small end.Big end is separated, half of which is integrated with the rod body, and the other half is rod cap. Connecting rod cap is assembled with the main crankshaft journal by bolts and nuts.
Connecting rod connects the piston and the crankshaft, and transmits the force exerted by the piston to the crankshaft, transforming the reciprocating motion of the piston into the rotational motion of the crankshaft. It is one of the main transmission components of automotive engines, which transmits the pressure of the expanding gas of the piston to the crankshaft, transforming the reciprocating linear motion of the piston into the rotational motion of the crankshaft, in order to output power.
Raw Material and Forging.
Connecting rod materials are mostly made of high-strength SAE1045 carbon steel, ASTM5140/40Cr carbon steel, etc., through quenching and tempering treatment to improve cutting performance and impact resistance. The hardness requirements for SAE1045 carbon steel are HB217-293 and ASTM5140/40Cr is HB223-280.
Blank of connecting rods is generally produced by forging, and there are two forms of blank: one is the separate forging of the body and cap; Another method is to forge the body and cap integrated, and then cut apart when machining or use an expansion process to break them during the processing. In addition, to avoid defects of the blank, 100% hardness measurement and flaw detection are required.
What kind of connecting rod is a good connecting rod?
The working temperature of the connecting rod is 90~100 ℃, and the rotational speed is 3000~5000r/min. In order to ensure the smooth entry of connecting rod forgings to automated precision machining production lines and the assembly accuracy of processed finished parts in the engine, and to maintain their ability to withstand extremely high frequency of tensile and compressive alternating stress during high-speed operation, so that the crankshaft is always in a balanced state, it is required that the connecting rod forgings have high strength and fatigue lifetime.
Connecting rod forgings should also meet the following technical and quality requirements while meeting the dimensional accuracy of the drawings:
1.Upspecified draft angel should be 3°- 5°, and upspecified R is between 2-5mm.
2.Forging surface should be smooth and free from defects such as cracks, folds, scarring, oxide skin (pits with a depth of>1mm).
3.Residual flash width on the parting surface ≤ 0.8mm.
4.The direction of the longitudinal section metal fiber should be along the centerline direction and consistent with the appearance, without any disorder or discontinuity, and without defects such as pores, cracks, folds, and non-metallic inclusions.
4.The hardness of quenching and tempering treatment ranges from 220 to 270HB.
5.Forgings have to be flaw detection inspection.
6.Repair welding is not allowed for defects on forgings.
Process:Forging.Machining.Heat treatment.Surface treatment.
Raw material:ASTM1035,ASTM1045,ASTM1021,ASTM1040,ASTM1320/20Mn2,ASTM1340/40Mn2,ASTM5120/20Cr,ASTM5140/40Cr,ASTM4119/20CrMo,ASTM4140/42CrMo,ASTM4135/35CrMo,ASTM4340/40CrNiMo,ST52-3/Q355/16M
Weight Range:0.1-200kgs
Certificate:ISO/TS16949
Heat treatment::Normalizing,Quenching and tempering
Inspection:Magnetic Powder Defects Test, Hardness Test, Dimension Test
Structure and function of connecting rod.
It is composed of three parts: big end of connecting rod,rod body and small end.Big end is separated, half of which is integrated with the rod body, and the other half is rod cap. Connecting rod cap is assembled with the main crankshaft journal by bolts and nuts.
Connecting rod connects the piston and the crankshaft, and transmits the force exerted by the piston to the crankshaft, transforming the reciprocating motion of the piston into the rotational motion of the crankshaft. It is one of the main transmission components of automotive engines, which transmits the pressure of the expanding gas of the piston to the crankshaft, transforming the reciprocating linear motion of the piston into the rotational motion of the crankshaft, in order to output power.
Raw Material and Forging.
Connecting rod materials are mostly made of high-strength SAE1045 carbon steel, ASTM5140/40Cr carbon steel, etc., through quenching and tempering treatment to improve cutting performance and impact resistance. The hardness requirements for SAE1045 carbon steel are HB217-293 and ASTM5140/40Cr is HB223-280.
Blank of connecting rods is generally produced by forging, and there are two forms of blank: one is the separate forging of the body and cap; Another method is to forge the body and cap integrated, and then cut apart when machining or use an expansion process to break them during the processing. In addition, to avoid defects of the blank, 100% hardness measurement and flaw detection are required.
What kind of connecting rod is a good connecting rod?
The working temperature of the connecting rod is 90~100 ℃, and the rotational speed is 3000~5000r/min. In order to ensure the smooth entry of connecting rod forgings to automated precision machining production lines and the assembly accuracy of processed finished parts in the engine, and to maintain their ability to withstand extremely high frequency of tensile and compressive alternating stress during high-speed operation, so that the crankshaft is always in a balanced state, it is required that the connecting rod forgings have high strength and fatigue lifetime.
Connecting rod forgings should also meet the following technical and quality requirements while meeting the dimensional accuracy of the drawings:
1.Upspecified draft angel should be 3°- 5°, and upspecified R is between 2-5mm.
2.Forging surface should be smooth and free from defects such as cracks, folds, scarring, oxide skin (pits with a depth of>1mm).
3.Residual flash width on the parting surface ≤ 0.8mm.
4.The direction of the longitudinal section metal fiber should be along the centerline direction and consistent with the appearance, without any disorder or discontinuity, and without defects such as pores, cracks, folds, and non-metallic inclusions.
4.The hardness of quenching and tempering treatment ranges from 220 to 270HB.
5.Forgings have to be flaw detection inspection.
6.Repair welding is not allowed for defects on forgings.
7.The quality deviation of each batch of forgings is ≤ 3%.
Comment Form