Categories of Electroplating Used for Auto
With people’s living standard constantly rising, Chinese auto industry shows rapid development tendency. Car parc grows annually. Meanwhile, requirements for auto security are higher and higher.
An auto consists of thousands of components. Components combine with each other and form parts. The parts connect and constitute an auto further. Due to improper combination, components may suffer from serious corrosion or damage. So, auto manufacturers must use electroplating to prevent auto components from being corroded.
To realize decoration, beautification, corrosion resistance and other special functions, electroplating is usually used. Besides oil painting, electroplating can be considered as the most important surface treatment technology used for auto.
Categories used for auto can be classified into three categories: protective decorative coating, protective coating and functional coating.
1. Protective decorative coating
Protective decorative coating has various colors, mainly used for auto marker, cover of water tank, bumper, door handle, window frame, wheel hub or ash pan. The coating should have bright appearance, even hues, delicate processing and it also should have good corrosion resistance after being electroplated. The protective decorative coating used for auto should not discolor or rust in the next 5-10 years. So, compared with electronic, machinery, hardware and light industry, the requirements for electroplating used for auto are higher.
2. Protective coating
Protective coating is also called as corrosion resistant coating. It does not has rigorous requirements such as protective decorative coating, while it also requires that the component should have good corrosion resistance. Protective coating includes zinc coating, cadmium plating, lead plating, zinc alloy and lead plating.
Protective zinc plating accounts for 70%~80% of total electroplating area on auto. Small stamping parts or even some large stamping parts and standard parts are almost plated with zinc. Protective zinc plating is one of the most important categories of electroplating on auto. What’s more, components contacting with accumulator should have resistance to sulfuric acid. The surface of components must be plated with lead or lead alloy.
3. Functional coating
(1) Tin coating, copper coating and lead-tin coating are used for improving weldability on the surface of components;
(2) Hard chrome, chrome having pine hole, hard anodized aluminum, thick nickel coating and nickel-phosphorus coating are used to improve hardness and abrasion resistance on the surface of metal.
(3) Iron coating and chromium coating are used to fix dimensions of components.
(4) Silver coating is used to improve electrical conductivity of metal.
(5) Lead-tin coating and lead-tin-copper coating are used to strengthen self-lubrication of bearing bush.
(6) Copper coating is used to prevent carburization.
Besides, steel oxidation, aluminum and aluminum oxidation, mold electroplating, plastic electroplating, surface coloration on metals and other surface treatment technologies are used for auto.
Electroplating used in auto industry is different from the same technology used in other industries. Because, some electroplated parts on auto have closed relationship with safety and reliability of auto. Electroplating also has direct influence on traffic accident.
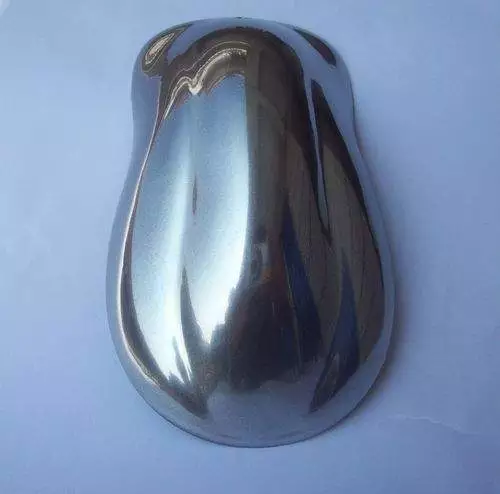